Risk Assessment on Occupational Health and Safety
[GRI 403-2 (2018), 403-7 (2018)]
EGCO Group encourages all power plants to adopt an internationally recognized occupational health and safety management system e.g. ISO 45001: 2018 to minimize and control potential risks to employees and relevant stakeholders. This aims to achieve the highest level of operational safety and foster trust and credibility with external stakeholders e.g. communities around the power plants, customers, and shareholders. Presently, EGCO Group’s power plants certified for ISO 45001:2018 include Khanom Power Plant, BLCP Power Plant, NED Power Plant, Star Energy Power Plant (SEG), Xayaburi Power Plant, Boco Rock Wind Farm, Nam Theun 2 Power Plant (NTPC), and Paju Power Plant. This certification signifies the company’s occupational health and safety advancement. Safety culture has also been encouraged to enhance knowledge, understanding, and awareness of workplace safety among its employees.
With the commitment to enhance its safety system, EGCO Group encourages all power plants to evaluate risks and opportunities of legal requirements regarding occupational health and safety as well as hazards from internal activities on a continuous and regular basis. The risk and opportunity assessment process are explained below.
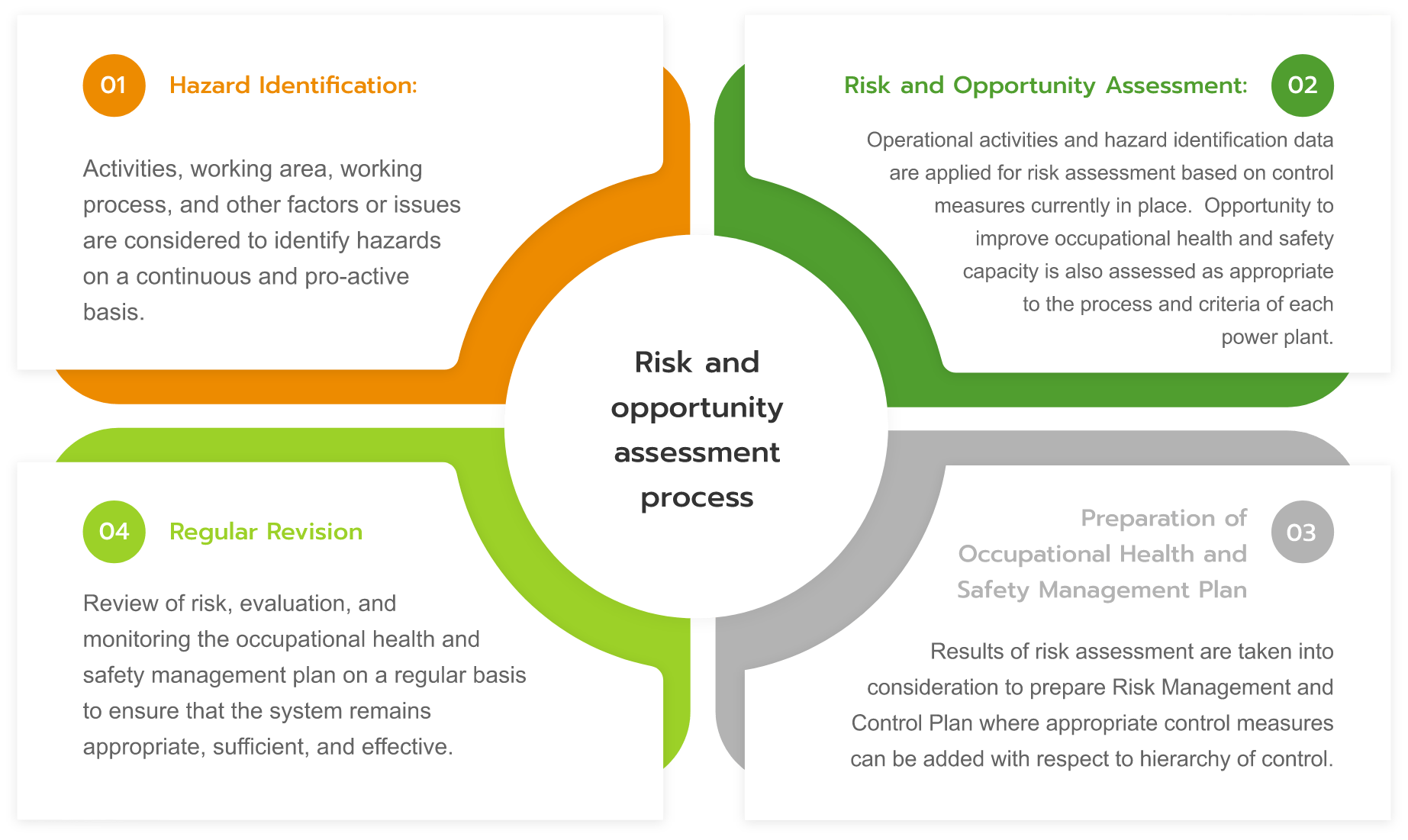
OHS risk and hazards assessments to identify what could cause harm in the workplace.
- Identify health & safety hazards along with the associated opportunities which may occur due to operation, activities, provision of products and services or logistics. Impacts can occur on the environment, employees, contractors, suppliers or any other relevant stakeholders such as neighboring communities.
Prioritization and integration of action plans with quantified targets to address those risks.
- Assess the identified OHS risk and opportunities, then rank each aspect and hazard (e.g., high, medium, low) such that mitigation measures or control procedures can be developed accordingly. Mitigation measures are intended to reduce possible risk to an acceptable level.
- Ensure risk assessment is reviewed on an annual basis or as-needed basis in order to mirror any changes implemented in the group, site, activity, products or services.
- Implement developed mitigation measures/ control procedures to manage the risk and opportunities.
- Communicated risk and opportunities in addition to mitigation measures/ control procedures to relevant personnel. Identified risks and opportunities can be used for the development of policies, objectives, targets and key performance indicators.
Evaluation of progress in reducing/preventing health issues/risks against targets
- Track performance against set goals and mitigation measures implemented are achieving the expected output and comply with regulation, thus, contributing to continual improvement.
Integration of actions to prepare for and respond to emergency situations.
- Identify potential emergency situations and responses to such situations in order to prevent and/ or mitigate health and safety impacts (i.e., to EGCO employees, relevant personnel or local communities) associated.
Internal inspections
- Develop an EGCO Group audit plan covering all facilities in order to assess the effectiveness of the implemented OHS management system. Such audit can be conducted once every 3 years depending on the performance level.
- Develop a site-specific audit plan covering all the elements of the OHS management system to identify site’s performance. This shall be conducted on an annual basis through the process of internal audits.
Procedures to investigate work-related injuries, ill health, diseases and incidents.
- Establish a clear process for reporting OHS incidents and responding to incidents in a timely manner. To share lessons learnt among sites to prevent and mitigate possible impacts and incidents from reoccurring. Hence, contributing to the improvement of the OHS performance.
OHS training is provided to employees and/or other relevant parties to raise awareness and reduce operational health & safety incidents.
- Ensure that all employees have the required knowledge, competency and understanding in performing their jobs responsibly to the environment and society.
- Establish and promote initiatives/ activities to advocate and raise OHS awareness among employees, contractors and applicable stakeholders. This shall cover information regarding the Group’s OHS policy, action programs to mitigate OHS risk and benefits of following an OHS management system.
OHS criteria introduced in procurement and contractual requirements.
- In terms of occupational health and safety management of suppliers, EGCO Group has identified occupational health and safety as one of EGCO Group’s essential sustainable issues and has communicated to suppliers the Suppliers’ Code of Conduct. It is one of the important issues to be investigated i.e., sustainable audit by suppliers themselves and supplier’s facilities inspection by EGCO Group. Such assessment results will be considered during the supplier selection process prior to and after working with EGCO Group.
Occupational health and safety management is one of the major factors that impact the quality of the working environment with our suppliers. It minimizes potential risks in the workplace and enhances the effectiveness and efficiency of the business operations. EGCO Group has established suppliers’ occupational health and safety standards, ensuring suppliers’ acknowledgment and adherence to these guidelines. Suppliers are evaluated using self-assessment questionnaires and site audits. Results of the assessment are taken into account during the supplier selection process before and during working with EGCO Group.